The Industry of the Future, also known as Industry 4.0 and defined as the fourth industrial revolution, represents a major transformation in the manufacturing sector, and offers promising prospects for the future of industry.
Born in Germany, this industrial revolution is made possible by the integration of advanced technologies such as artificial intelligence (AI), the Internet of Things (IoT), big data, machine learning (MachineLearning) and many other emerging technologies.
By enabling intelligent interconnection and the digitization of industrial processes, Industry 4.0 paves the way for significant improvements in productivity, energy efficiency and environmental sustainability.
However, behind this promising vision lie major challenges. Implementing this industrial revolution can be hampered by obstacles such as financial constraints, lack of technical skills and organizational constraints.
I] Understanding the whole concept
Industry 4.0 marks the convergence of the physical and digital worlds.
The combination of these technologies promotes the interconnection of information, enabling manufacturers to save time and gain greater control over their value chain.
Industry 4.0 therefore enables, increased automation of production processes, predictive maintenance to reduce equipment downtime, improved product quality and reduced manufacturing errors through the use of machine learning algorithms such as Machine-Learning (ML).
What’s more, integrating high-tech IoT devices into smart factories boosts productivity and improves product quality, while reducing production costs.
Industry 4.0 is not just a technological revolution, it also has social, political and environmental implications. It raises the question of employment in a context where automation is becoming increasingly important.
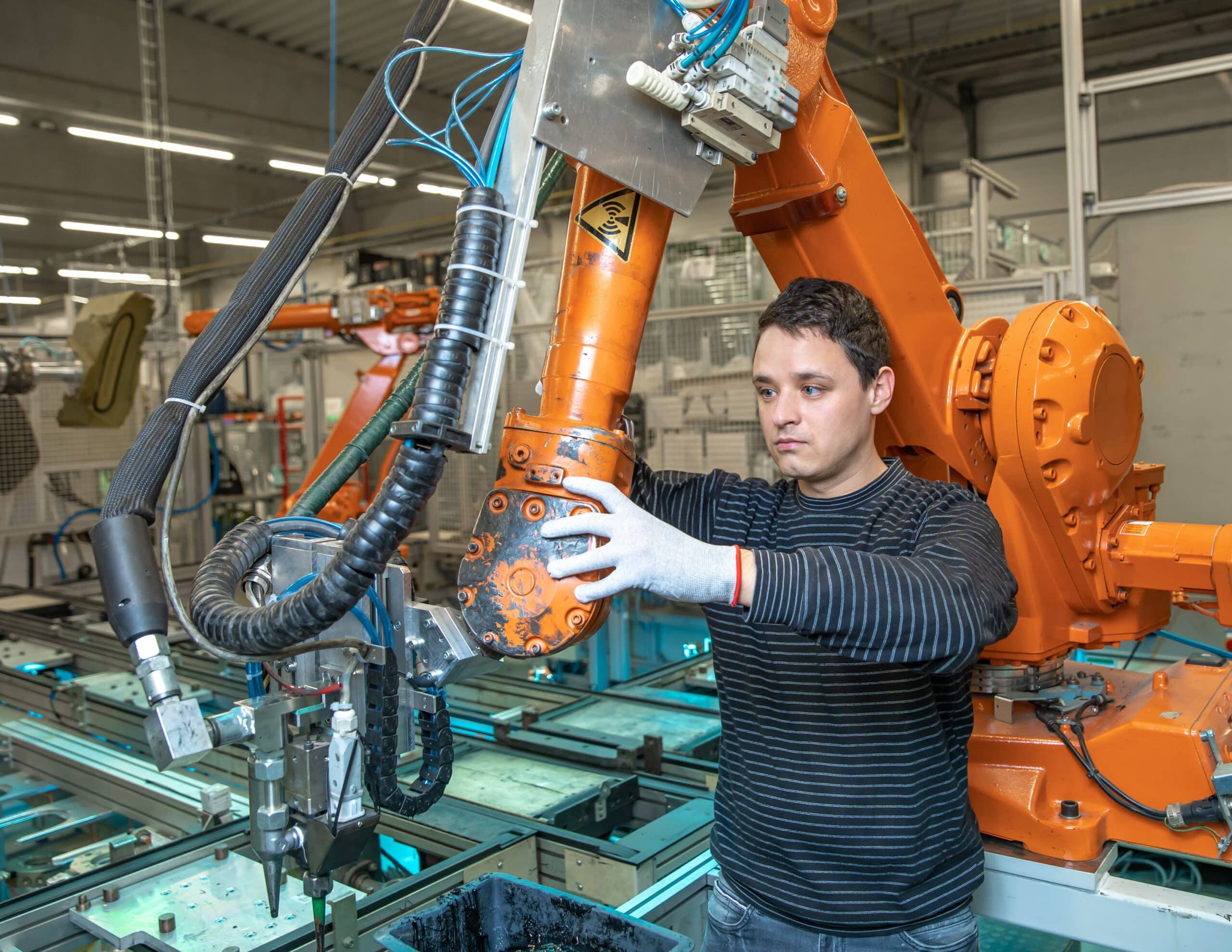
Supporting current employees and training future employees are major issues to be taken into account in this transformation. It is essential to think about the place of people in this new way of producing.
II] Integrating digitalization into corporate strategy
In the era of Industry 4.0, digitalization occupies a central place in the strategy of the modern company. Having grasped the overall concept of Industry 4.0, it becomes essential for organizations to effectively integrate digitalization into their strategy to remain competitive in today’s marketplace.
Industry 4.0 is characterized by the intelligent interconnection of all links in the production chain thanks to the various technologies mentioned above. This enables machines to produce autonomously thanks to a Machine-to-Machine (M2M) protocol, and to adjust in real time to demand, thus improving production efficiency and inventory management.
To integrate digitalization into their strategy, companies need to take the following factors into account:
1. Define a clear vision: The first step in integrating digitalization into corporate strategy is to define a clear vision of the objectives to be achieved. This involves understanding how digitization can improve processes, increase operational efficiency, and meet customer expectations, while keeping in mind the benefits and challenges of digital transformation.
2. Alignment with market needs: The integration of digitalization must be aligned with market needs and customer expectations. It is essential to understand how digital technologies can enhance the customer experience, increase responsiveness to market demands and create a unique value proposition.
3. Invest in key technologies : to effectively integrate digitalization, companies need to invest in key Industry 4.0 technologies, such as IoT, AI, data analytics and automation. These technologies provide the tools needed to collect and analyze data in real time, optimize production processes and improve decision-making.
4. Employee training and awareness: Integrating digitalization requires a cultural change within the company. Employees need to be made aware of the importance of digital transformation and trained in the new technologies, so that they can use them optimally and actively contribute to the implementation of the digitalization strategy.
5. Integration into existing processes: Digitization is not about completely replacing existing processes, but rather about improving them by using digital technologies to make them more efficient and agile. Seamlessly integrating digitalization into existing operations is essential to optimize productivity and minimize disruption.
By effectively integrating digitalization into their strategy, companies can reap numerous benefits, such as improved operational efficiency, product customization, lower production costs and greater competitiveness in the marketplace.
III] Training, transforming and uniting employees
The emergence of Industry 4.0 is a societal revolution that is overturning production methods, corporate hierarchies, skills and professions. To ensure a successful transition to this new industrial era, it is imperative to prepare and support employees in the face of unprecedented technological change.
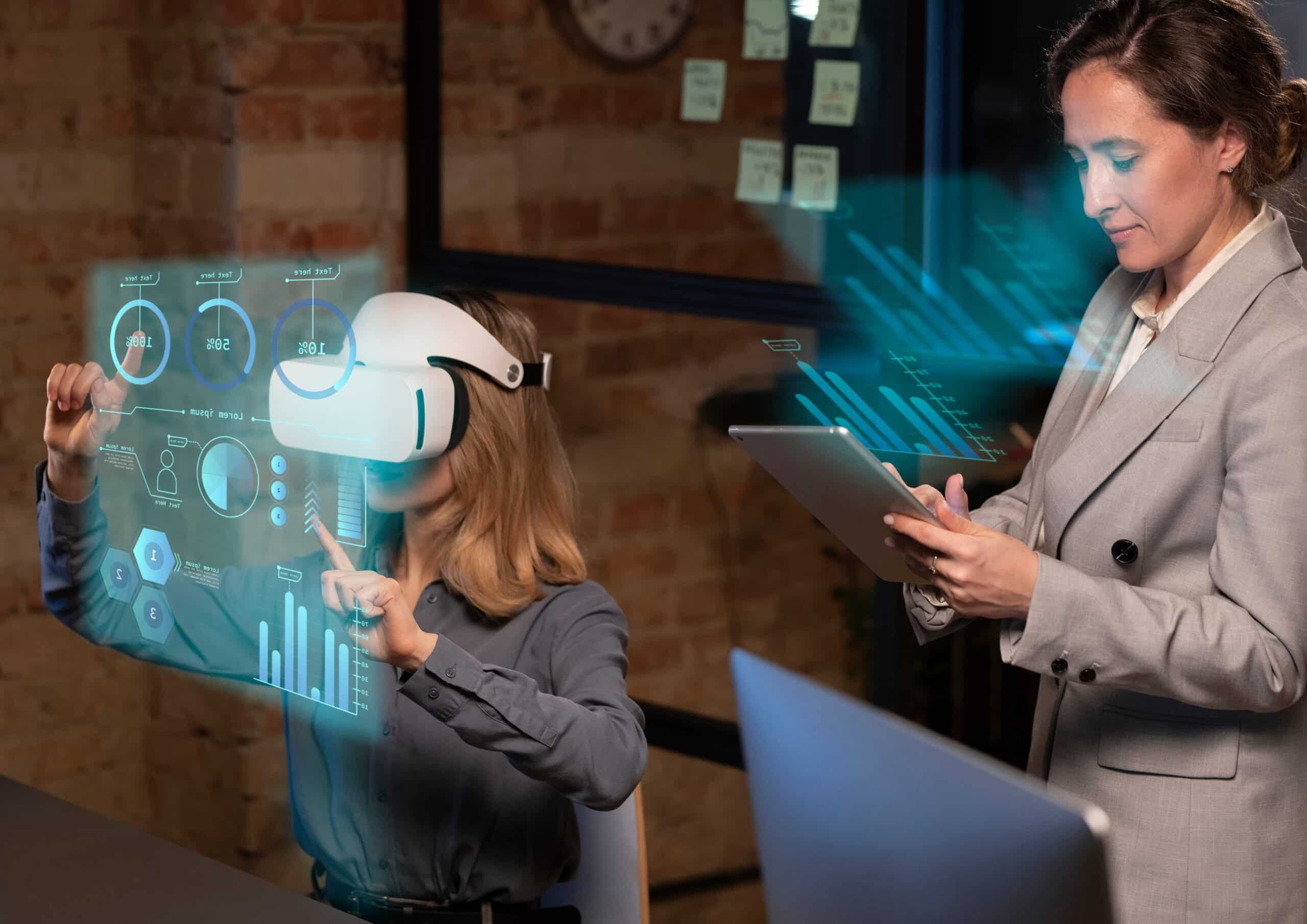
This involves training, transforming work practices, and getting employees to embrace change.
1. Training : Raising employee qualifications is essential to anticipate and meet the challenges posed by Industry 4.0. Repetitive and dangerous tasks will give way to process monitoring and improvement missions, requiring specific skills. Digital technology is reshaping the way we work, requiring advanced technical skills, particularly in programming, web development, data processing and collection, and everything else inherent in new technologies.
2. Transformation: Digital technology doesn’t replace work, it reshapes it. Work organization is evolving towards new forms of team cooperation and self-regulation, demanding greater autonomy and responsibility from employees. Their support is essential, and for this to happen, they must be involved in the management of transformations, in consultation with their representatives. The shift towards Industry 4.0 must be accompanied by a reinvention of existing professions and the emergence of new ones, requiring a skilled, competent workforce trained in the new technologies.
3. Employee understanding and buy-in: To successfully integrate Industrie 4.0, it is essential that employees understand the challenges of this transformation. Communication and awareness-raising are therefore vital to create buy-in and reduce resistance to change. Companies need to provide clear information on the objectives, benefits and opportunities associated with Industrie 4.0. This will help create an environment conducive to employees learning and adapting to the new technologies and working methods.
4. Supply chain optimization: Interconnected production systems also facilitate integration with supply chains and trading partners. Real-time data on production, inventory and demand enable more efficient supply management, better synchronization of deliveries, and reduced logistics costs. This contributes to a more agile and responsive supply chain, which is essential to remain competitive in the global marketplace.
IV] Ensuring interconnection at all production levels
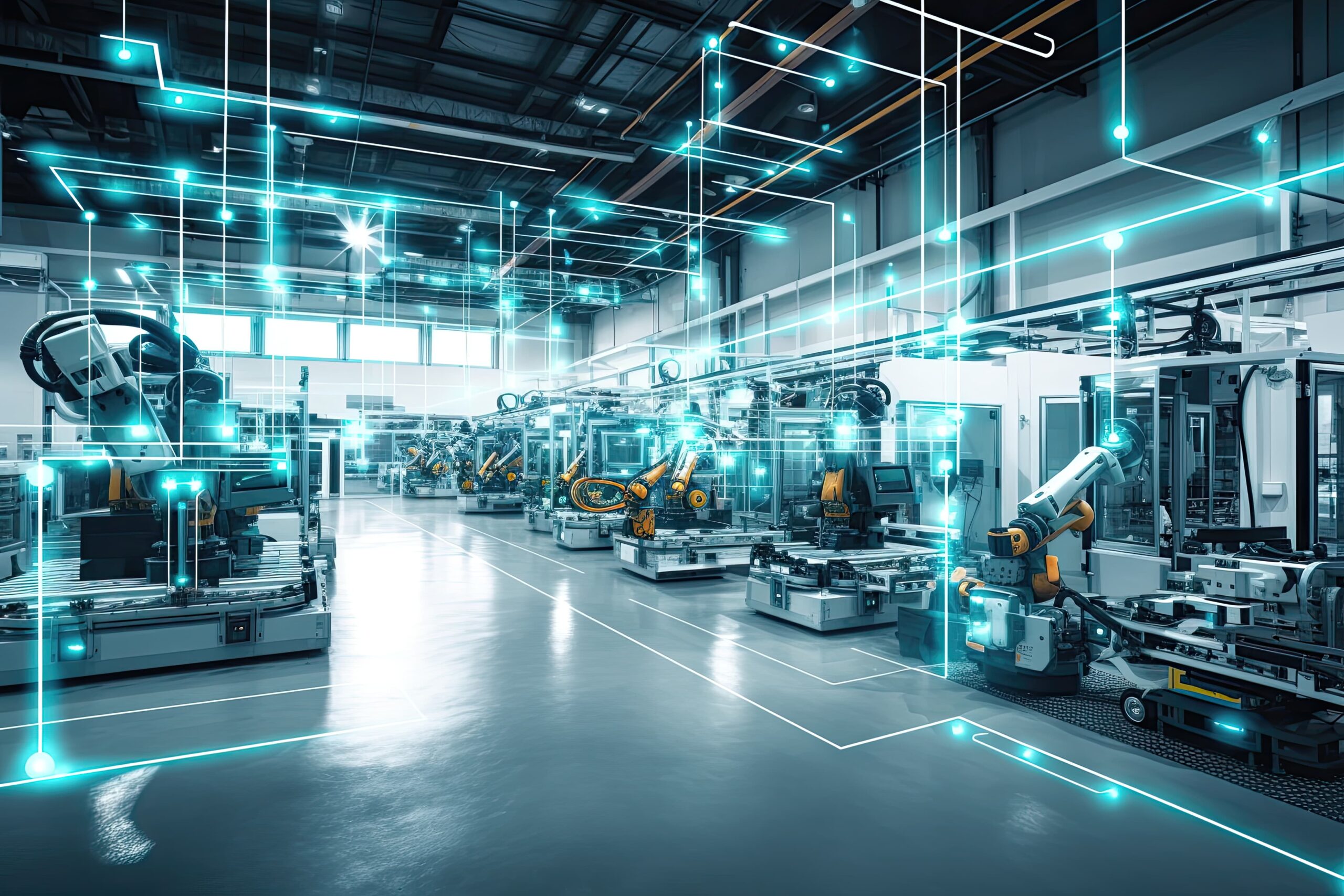
In Industry 4.0, ensuring interconnectivity at all production levels is crucial to the successful transformation of industrial companies.
This interconnection relies on the use of IoT, real-time data analysis, and the introduction of cyber-physical systems. Here are the reasons why this interconnection is necessary:
- Improved efficiency and productivity: Interconnected production systems enable seamless, real-time communication between different equipment, machines and operators. This helps to optimize process coordination, quickly identify bottlenecks and production problems, and make informed decisions to improve overall efficiency. Real-time data also facilitates production planning and management, enabling us to better meet customer demand and increase overall productivity.
- Optimal decision-making: The interconnection of computer systems (IS) and machines makes it possible to collect massive amounts of data from different sources. This data is then analyzed in real time thanks to IoT and Big Data, generating valuable information for decision-making. This enables managers to gain a global view of production, identify trends, anticipate potential problems, and make decisions based on reliable, up-to-date data. This contributes to greater responsiveness and more efficient production management.
- Greater customization and flexibility: interconnection at all production levels enables the creation of more flexible and adaptable production lines. Thanks to real-time analysis of customer data, companies can better understand consumer preferences and needs. This enables them to further customize products and services to meet specific market demands. Greater flexibility in production also means they can adapt quickly to changes in demand, and introduce new products more rapidly.
- Supply chain optimization: Interconnected production systems also facilitate integration with supply chains and trading partners. Real-time data on production, inventory and demand enable more efficient supply management, better synchronization of deliveries, and reduced logistics costs. This contributes to a more agile and responsive supply chain, which is essential to remain competitive in the global marketplace.
V] Managing and processing data in real time
In the context of Industry 4.0, interconnection at all production levels is of crucial importance to realize the full benefits of this fourth industrial revolution. However, successful interconnection cannot be achieved without efficient management and agile real-time data processing.
Indeed, implementing Industry 4.0 in a company requires a solid infrastructure to collect, manage and analyze the data generated at every stage of the production process.
Managing and processing data in real time is essential to ensure that Industry 4.0 runs smoothly within a company.
Here’s why this step is crucial:
1. Process optimization: Real-time collection and analysis of data from sensors, machines and systems within the plant enables in-depth understanding of operations. This helps identify inefficiencies, bottlenecks and opportunities for optimizing production processes. By adjusting production parameters in real time according to current data, companies can improve efficiency, reduce downtime and minimize waste.
2. Predictive maintenance: Thanks to real-time monitoring of equipment and machines, the data collected can be used to predict maintenance requirements. Analysis models can anticipate potential breakdowns by detecting abnormal patterns in the data. This enables proactive maintenance planning, avoiding unscheduled downtime and maximizing equipment availability.
3. Production customization: The ability to rapidly collect and analyze data in real time enables companies to respond to changing customer demands and customize production. By adjusting production parameters according to individual specifications, companies can deliver tailor-made products while maintaining efficient production.
4. Quality improvement: Real-time analysis of production data enables rapid detection of quality variations and identification of potential defects. This enables companies to intervene immediately to correct problems, reducing scrap and improving overall product quality.
5. Informed decision-making: The availability of real-time data enables decision-makers to make informed, fact-based decisions. Real-time information provides continuous visibility of production performance, enabling managers to react quickly to challenges and opportunities.
Successfully integrating Industry 4.0 into a company requires effective real-time data management and processing. The ability to collect, analyze and exploit data from a variety of sources throughout the production process is essential to optimize operations, improve quality, maintain predictive maintenance and respond agilely to market demands.
Real-time data is at the heart of the complete interconnection of systems and operations, enabling companies to realize the full benefits of the fourth industrial revolution.
VI] Prioritizing cyber security and data protection
As Industry 4.0 continues to transform businesses by making them more interconnected and digital, prioritizing cybersecurity and data protection becomes an imperative necessity to ensure the success and security of this transition.
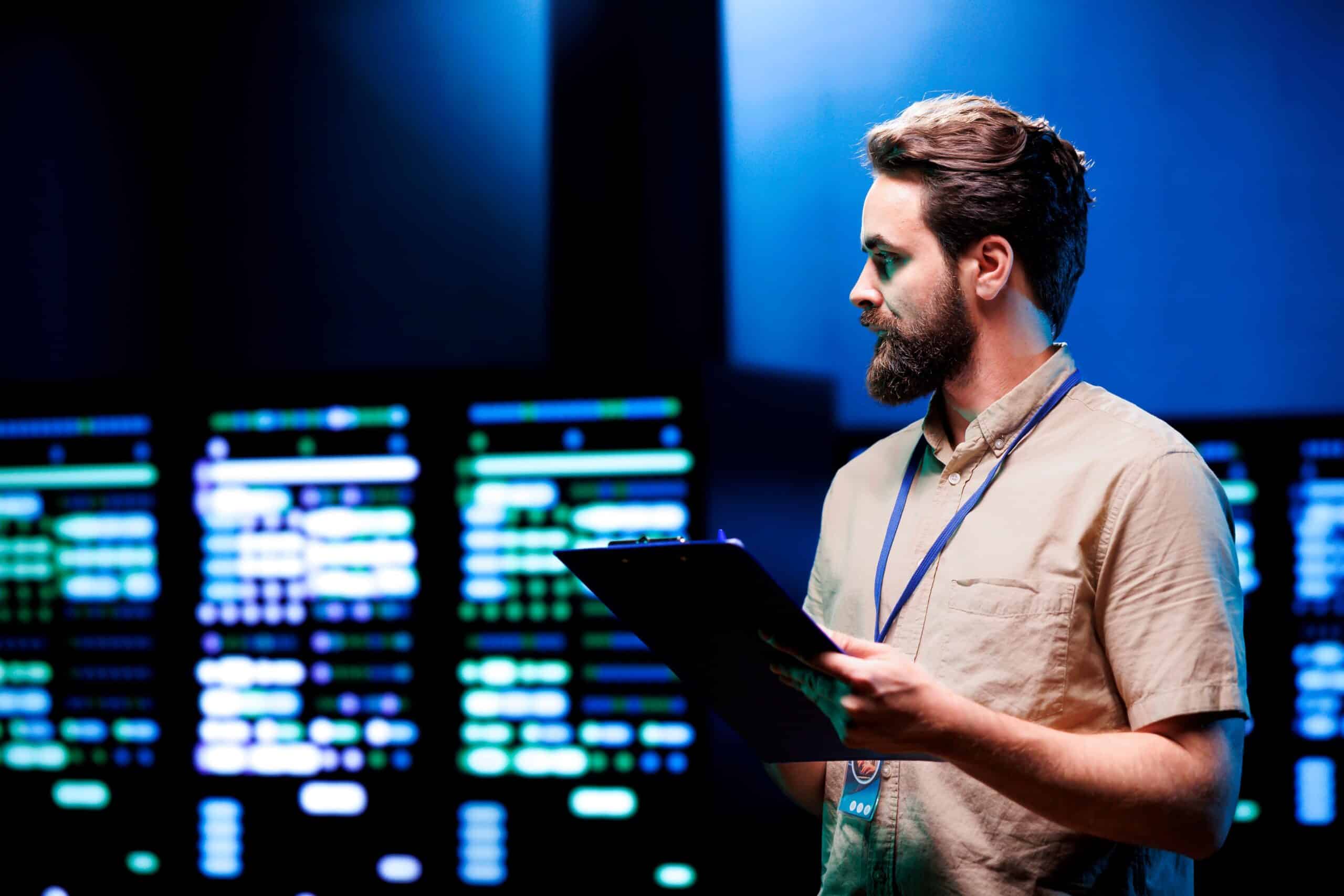
The rise of Industry 4.0 has led to an unprecedented convergence between information systems (IT) and operational systems (OT). However, this interconnection also presents security risks. Critical infrastructures such as factories, power grids and distribution systems are becoming potential targets for cyberattacks and malicious actors.
In the context of Industry 4.0, where data circulates in real time at all levels of production, prioritizing cyber security becomes crucial to protect this data from growing threats. Real-time data is a valuable asset, but it is also becoming a prime target for cybercriminals.
Companies need to implement proactive security measures to prevent cyber-attacks, protect data integrity and ensure business continuity. This involves implementing robust security controls, identity and access management, continuous system monitoring and raising employee awareness of IT security best practices.
Data protection is a major concern in the context of Industry 4.0.
Companies collect and process massive amounts of data in real time to optimize operations, improve quality and make decisions based on in-depth analysis. However, this data is vulnerable to security breaches, leaks and theft.
The implementation of advanced security protocols, such as data encryption, access monitoring and rigorous authorization management, is essential to protect data against potential threats.
The importance of prioritizing cybersecurity and data protection extends beyond data security. By securing IT/OT interconnections and protecting data, companies are also helping to guarantee operational continuity and production stability. This stability is essential for optimizing production facilities.
By implementing robust security measures, companies can create an environment conducive to innovation, efficiency and competitiveness, while minimizing the risks associated with cyber threats.
VII] Optimizing the production tool
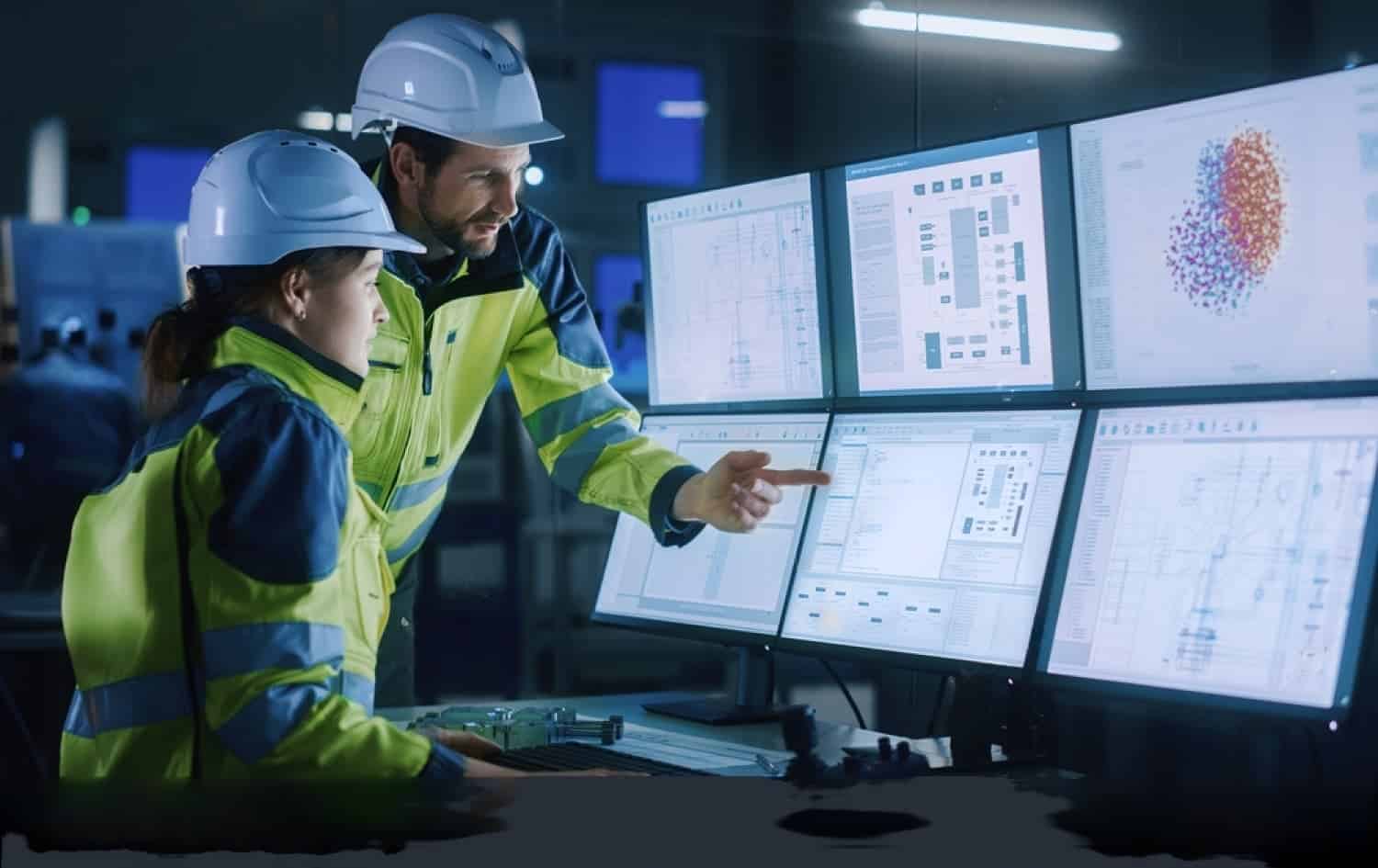
Production tool optimization is an essential part of the transition to Industry 4.0. This step aims to maximize the efficiency, flexibility and productivity of manufacturing processes by strategically exploiting innovative technologies and concepts.
Here are 10 examples of key Industry 4.0 tools that help optimize the production tool:
- The Industrial Internet of Things (IIoT): IIoT enables machines and equipment to monitor, communicate and share data in real time. By collecting and analyzing data from sensors and connected devices, manufacturers can optimize machine performance, anticipate breakdowns and reduce unplanned downtime.
- Machine Learning (ML): Integrating ML into production processes improves decision-making by analyzing voluminous data and identifying trends or patterns. This can lead to significant improvements in quality management, optimization of production parameters and waste reduction.
- MES ( Manufacturing Execution System) software: MES systems enable production to be supervised and controlled in real time, facilitating the planning, execution and monitoring of operations. This software contributes to better coordination between the different stages of production, reducing changeover times and improving resource utilization.
- The digital twin: The concept of the digital twin consists in creating a virtual replica of a physical object, be it a product, a machine or even an entire factory. This makes it possible to simulate production scenarios, test modifications before they are actually implemented, and optimize design and processes. They also make it possible to experiment with energy efficiency scenarios without disrupting actual production.
- Augmented Reality (AR) has many applications in Industry 4.0, including operator training, computer-aided maintenance and real-time data visualization. It improves operational efficiency by providing contextual information directly to workers in the field.
- Cloud Computing: Cloud services offer a flexible infrastructure for data storage and processing, giving companies rapid access to the resources they need to optimize operations.
Data can be shared and analyzed from a variety of facilities, fostering collaboration and innovation.
- Collaborative robotics: Collaborative robots, also known as cobots, work in collaboration with humans in a production environment.
They can perform repetitive, dangerous or precision-intensive tasks, freeing workers for more complex and creative tasks.
- 3D printing: 3D printing is revolutionizing manufacturing by enabling complex parts to be created quickly and efficiently.
This technology offers great flexibility in the design and production of prototypes, custom components and spare parts, which can help reduce production times and costs.
- Advanced data analysis: Advanced data analysis, also known as industrial analytics, extracts valuable information from the data generated by machines and production processes.
Using sophisticated algorithms, manufacturers can identify trends, anomalies and optimization opportunities, leading to better decision-making and continuous improvement.
- Cyber-physical systems (CPS): CPS are systems integrating IT, communication and control components with the physical world. They enable real-time interaction between equipment, sensors and actuators, creating intelligent, responsive production environments. CPSs enable automated decision-making and dynamic adjustment of processes to optimize performance.
By implementing these tools synergistically, companies can create more agile, adaptable and high-performance production environments. Optimizing production tools within the framework of Industry 4.0 makes it possible to respond effectively to the challenges of competitiveness, product customization and customer satisfaction, while fully exploiting the potential of digital and connected technologies.
VIII] Improving energy efficiency
Energy efficiency plays a crucial role in the context of Industry 4.0, where data plays a key role in transforming and optimizing industrial operations.
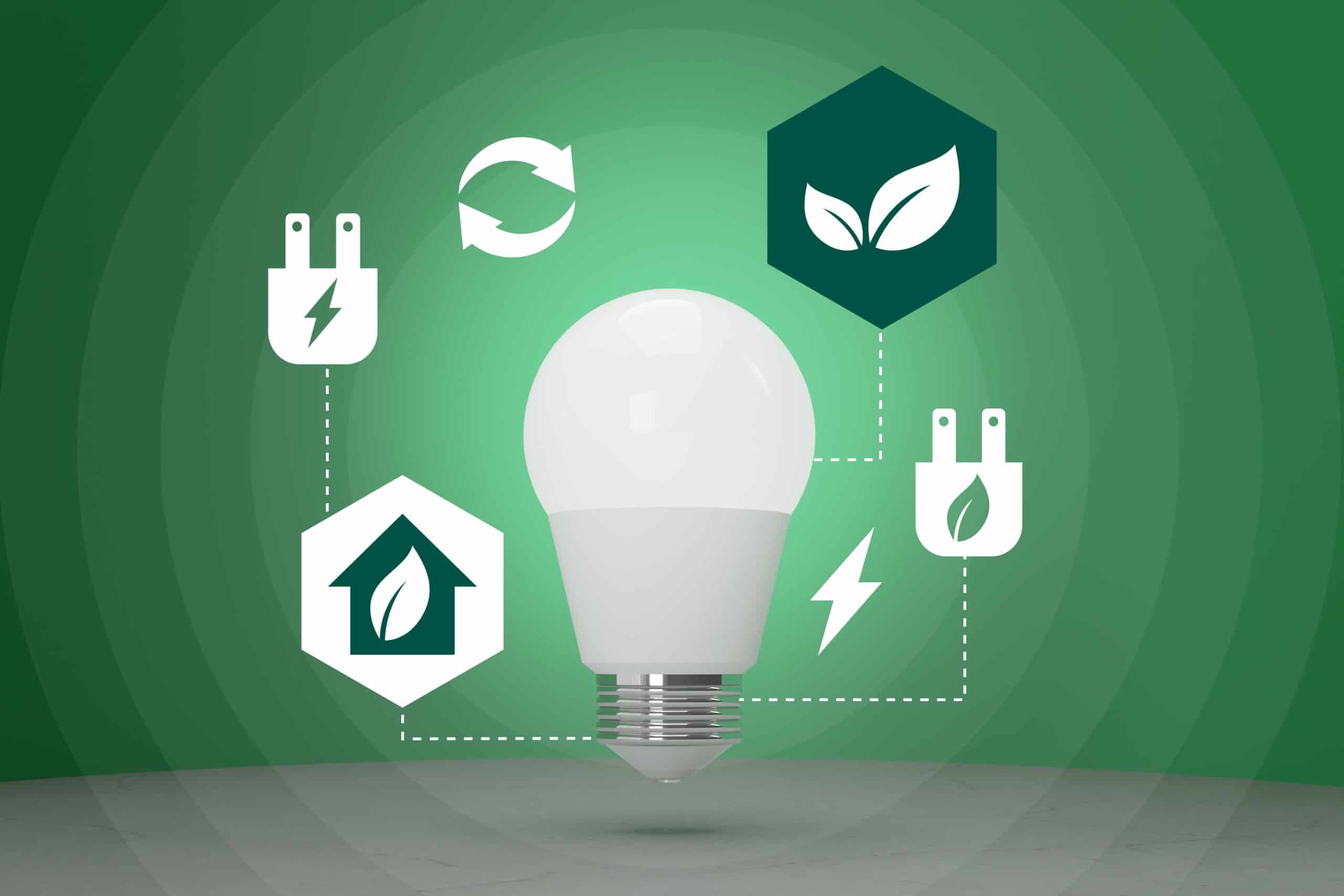
Industrial companies are faced with the challenge of reducing their energy consumption while maintaining high production levels and meeting environmental targets. Fortunately, advances in Industry 4.0 offer new opportunities to significantly improve energy efficiency.
At the heart of this transformation is the use of massive data collected from sensors and connected devices. Data is collected in real time, interpreted using advanced analysis tools and integrated into predictive models. This makes it possible to identify bottlenecks and inefficiencies in production processes, and make adjustments to minimize energy consumption.
The advantages of this approach are manifold, and here are just a few examples:
- Detecting inefficient processes: Data can be used to identify production processes that consume a disproportionate amount of energy in relation to the results obtained. By better understanding these energy bottlenecks, companies can make targeted improvements to reduce consumption.
- Production and logistics optimization: Real-time data enables companies to monitor and optimize production according to variations in demand, environmental conditions and energy costs. This can involve adjustments in planning, logistics and resource utilization to minimize energy consumption.
- Predictive maintenance: Data can be used to anticipate equipment maintenance requirements. By anticipating potential breakdowns, companies can avoid unplanned downtime, contributing to more efficient energy use.
- Dynamic demand management: Data can be used to adjust energy demand in line with fluctuations in electricity prices and availability. This can involve shifting energy-intensive processes to periods when energy is cheaper and more plentiful.
- Optimizing energy and raw materials consumption: Industry 4.0 offers the possibility of a global vision of the plant and its equipment, thanks to the interconnection of systems. This visibility enables better management and optimization of energy and raw materials consumption. Companies can adjust production processes in real time to maximize energy efficiency and minimize waste. This intelligent optimization of resources helps reduce costs and mitigate the environmental impact of production.
- Logistics optimization: Industry 4.0 enables better logistics management thanks to the interconnection of all links in the production chain, made possible by the IoT. Algorithms can calculate optimal delivery routes to avoid congestion, interruptions and delays, improving the flow of goods. This optimization of logistics helps to reduce inefficiencies, cut waiting times and minimize energy consumption associated with product transport and distribution.
By adopting these data-centric approaches, industrial companies can significantly reduce their energy consumption while improving their operational efficiency. This move towards smarter, more efficient energy management is a concrete example of how Industry 4.0 is transforming the way companies tackle energy and environmental challenges.
Industry 4.0 is emerging as a genuine revolution in the manufacturing sector, guided by the strategic adoption of digital technologies, advanced automation and smart connectivity. This transformation has been characterized by the integration of the internet and digital technology into production and management processes.
Energy efficiency is one of the major benefits of Industry 4.0, enabling companies to reduce their energy consumption, minimize their carbon footprint and contribute to the fight against climate change.
Thanks to real-time data analysis, predictive maintenance and resource optimization, companies can improve their operational performance while reducing their environmental impact.
However, as Industry 4.0 continues to take shape, new perspectives are emerging on the horizon. Industry 5.0 is already taking shape as an even more profound evolution, introducing the concept of enhanced collaboration between man and machine.
While the fourth industrial revolution marked the beginning of automation and digitization, the fifth revolution goes a step further by integrating unique human capabilities such as creativity, critical thinking and adaptability.
Industry 5.0 places workers at the heart of the production process, viewing them not just as a resource, but as a valuable investment.
Technology is seen as a tool to enhance and support human work, rather than replace it.
Looking to the future, Industry 5.0 ushers in a new era of man-machine collaboration and industrial progress. It offers the promise of an enhanced symbiosis between technology and people, creating unlimited potential for significant advances in production, energy efficiency and sustainability.